What you want to know is not the mold manufacturing process but the injection molding product production process?
Please click: https://www.plasticmetalmold.com/professional-injection-moulding-services/
Service Description
As one of our main businesses, we offer a wide range of customised production of injection moulds in different sizes. We can provide the best service to our customers from the initial design, mould manufacturing and testing to the after-sales process.
An injection mold is a tool for manufacturing plastic products; it is also the tool that gives plastic products a complete structure and precise dimensions. Injection molding is a processing method used for mass production of some complex shaped parts. Specifically, hot, molten plastic is injected into the mold cavity under high pressure from an injection molding machine, and after cooling and curing, the molded product is obtained.
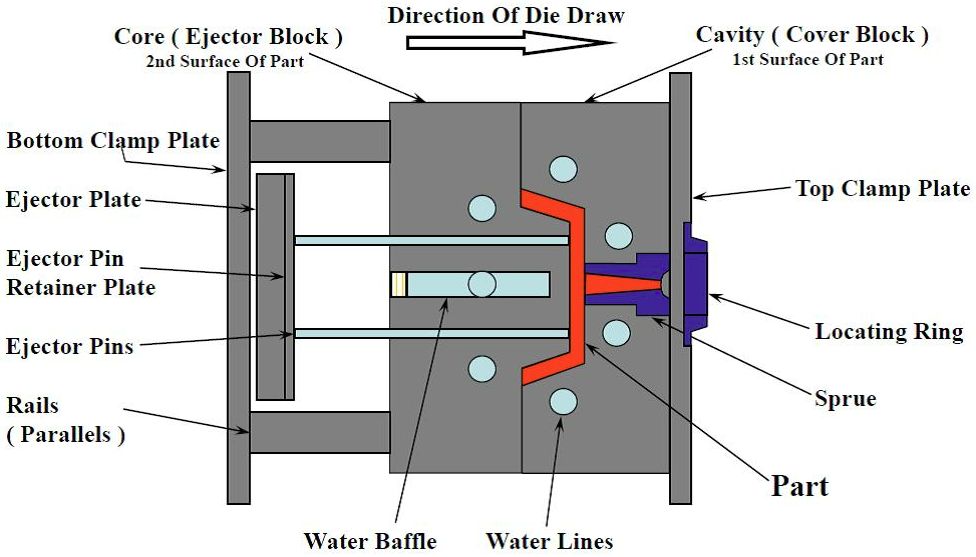
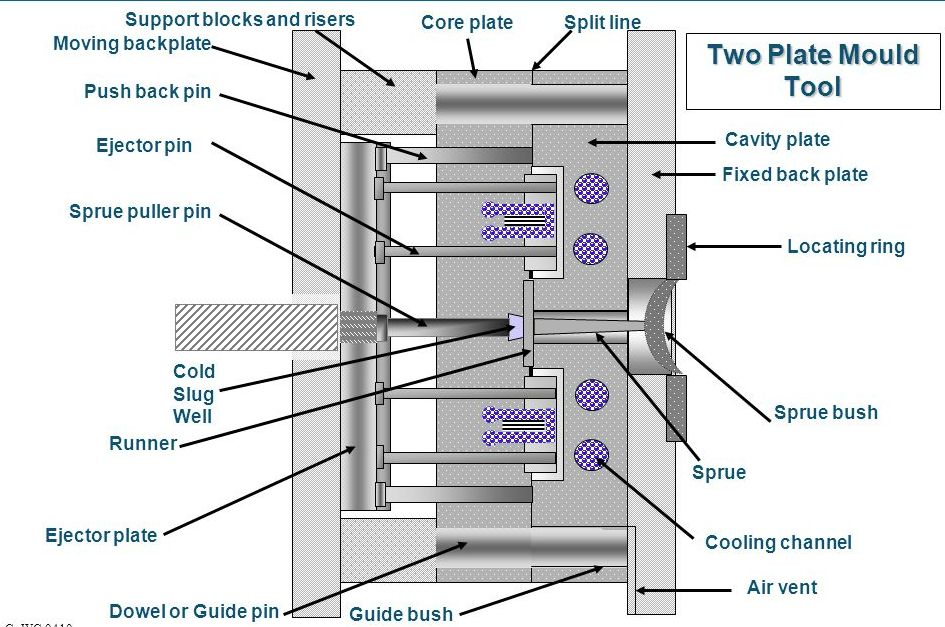
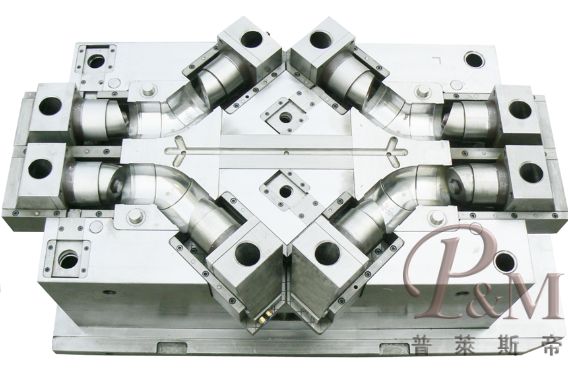
Injection molds according to the molding characteristics of thermoset plastic molds, thermoplastic plastic molds two; according to the molding process, they are distinguished into transfer molds, blow molds, casting molds, thermoforming molds, hot pressing molds (compression molds), injection molds, etc., where hot pressing molds for material overflow can be divided into overflow type, half overflow type, no overflow type three, injection molds for casting system can be divided into cold runner molds, hot runner molds two; according to the loading and unloading method can be divided into mobile, fixed two.
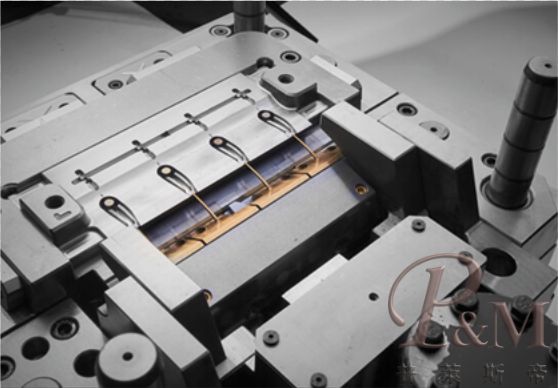
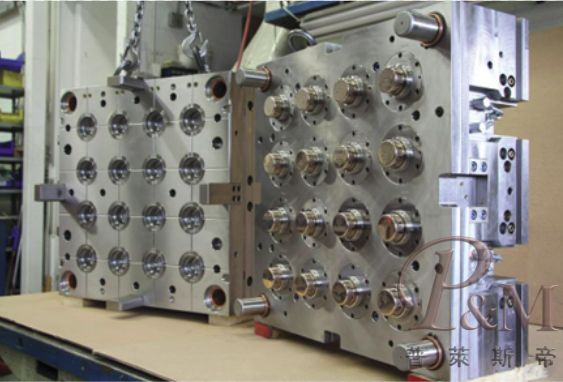
Service Process
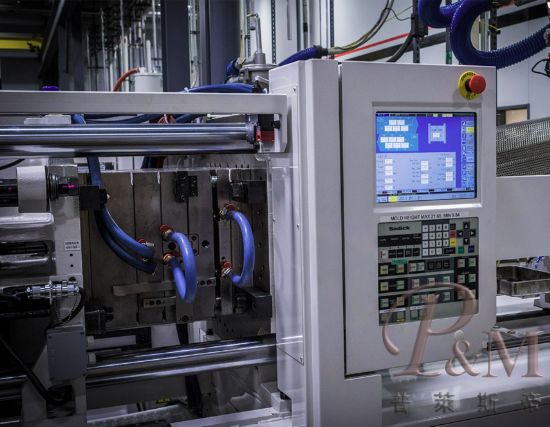
The process of injection mould making is tedious and complicated, it seems to be simple and requires many processes behind the operation. The injection mould making process mainly includes: accepting customer's custom requirements, engineering team mould design, mould manufacturing, mould inspection and trial mould, mould modification and repair, mould maintenance. The following Ningbo P&M will take you through the process one by one.
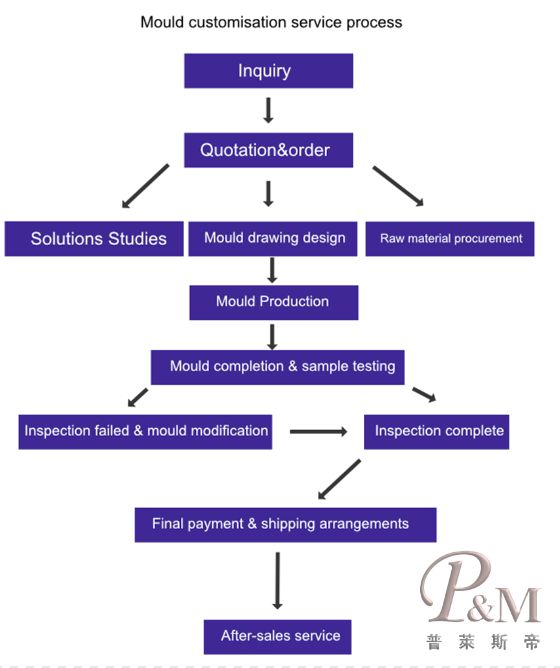
1 Order comfirm&preparation
Customer place the order, analysis of product structure, material and processing technology, decision on injection molding machine equipment
Plastic mold making, first of all, the customer engineering staff to provide product drawings to the mold manufacturer, the manufacturer through the molding plastic production task requirements, the process of collecting, analyzing, digesting product data, this for customer customization.
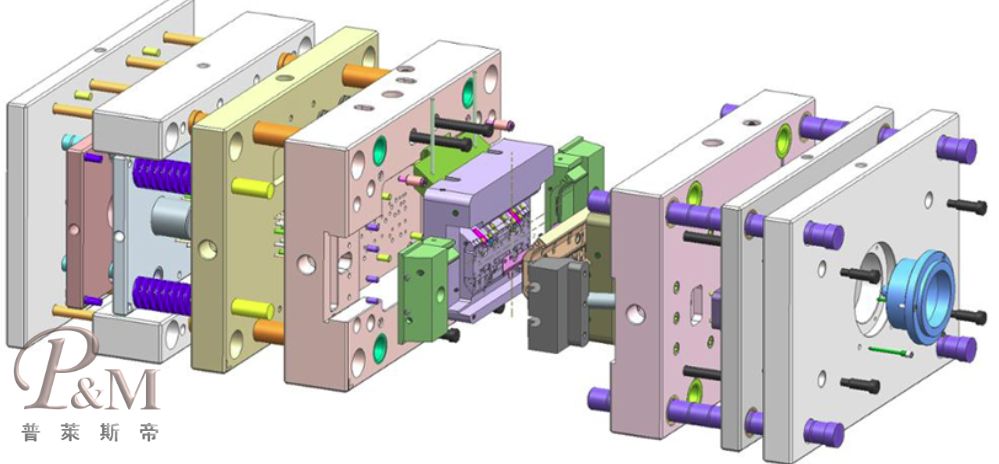
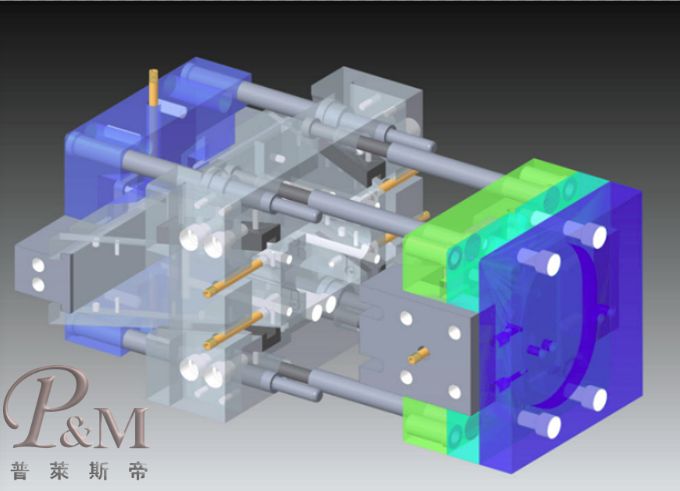
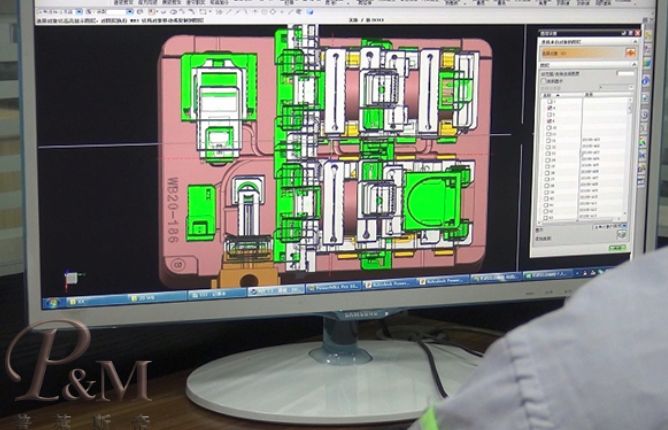
2 Design of mold (mold base, components), drawing
Before the designing of the mold, we need understand the use of parts, technology, dimensional accuracy and other technical requirements. For example, what are the requirements of plastic parts in terms of appearance, color transparency, and performance, whether the geometry, slope, and inserts of plastic parts are reasonable, the allowable degree of molding defects such as fusion marks and shrinkage, and whether there is post-processing such as painting, plating, silk-screening, and drilling.
Estimate whether the molding tolerance is lower than the tolerance of the plastic parts, and whether the plastic parts can be molded to meet the requirements. In addition, to understand the plasticization of plastic and molding process parameters.
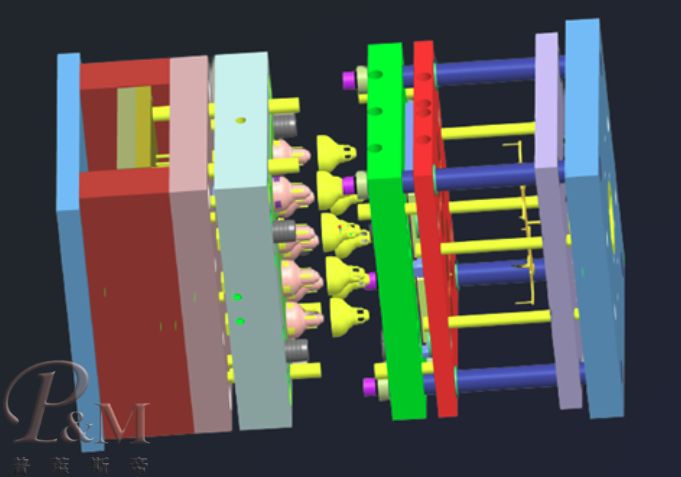
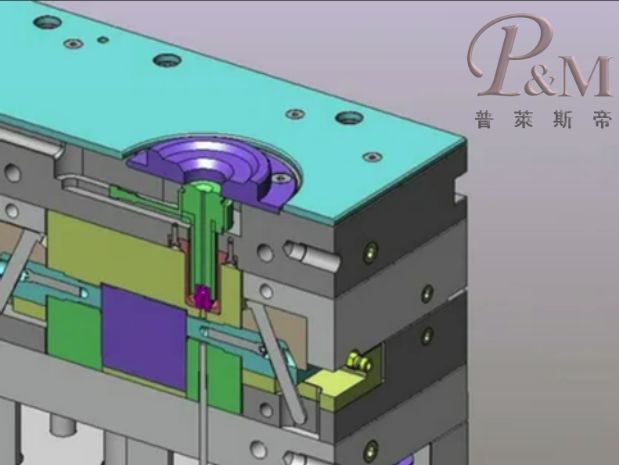
3. Material selection
Also we will figure out the requirements of glue feeding method, brewer model, plastic material properties, mold structure type, etc.
The molding material should meet the strength requirements of plastic parts, have good fluidity, uniformity and isotropy, and thermal stability. According to the use of plastic parts and whether post-processing, molding materials should meet the requirements of dyeing, metal plating conditions, decorative properties, necessary elasticity and plasticity, transparency or reflective properties, gluing (such as ultrasonic) or welding.
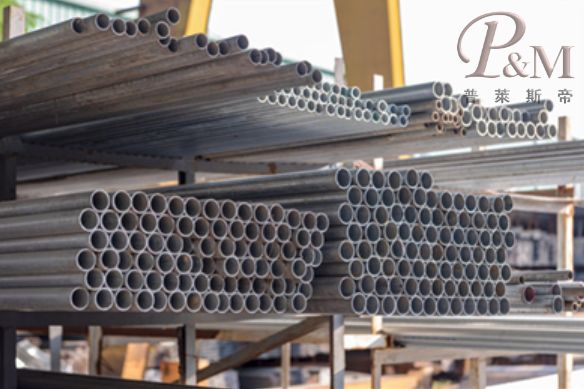
Molded parts refer to direct plastic contact and molding products, such as cavities, cores, sliders, inserts, inclined planes, side dies, etc.
The material of molded parts is directly related to the quality and durability of the mold and determines the appearance and internal quality of molded plastic products.
The principle of material selection is: based on the type of molded plastic, product shape, dimensional accuracy, product appearance, quality and usage requirements, production batch size, taking into account the cutting, polishing, welding, etching, deformation, wear resistance and other material properties, taking into account the economy and production conditions of the mold and processing methods, to choose different types of steel. There are many mold steels, and the choice of mold material can be determined by the nature of the product and the number of products.
(1) for molding transparent plastic products, the cavity and core should use high-quality imported steel with high mirror polishing performance, such as 718 (P20 + Ni class), NAK80 (P21 class), S136 (420 class), H13 class steel, etc.
(2) For the requirements of product appearance quality, long service life, mass production of molds, the cavities should use high quality imported steel with high mirror polishing performance, such as 718 (P20 + Ni class), NAK80 (P21 class), etc. The core can be used in the low-grade imported steel type P20 or P20 + Ni.
(3) for small and precision mold products, appearance quality requirements in general, its molding parts are used in the imported medium-grade steel grade P20 or P20 + Ni.
(4) for no appearance quality requirement of the internal structure of parts, forming materials on the steel also no special requirement of the mold, can choose the low grade steel P20 or P20 + Ni class
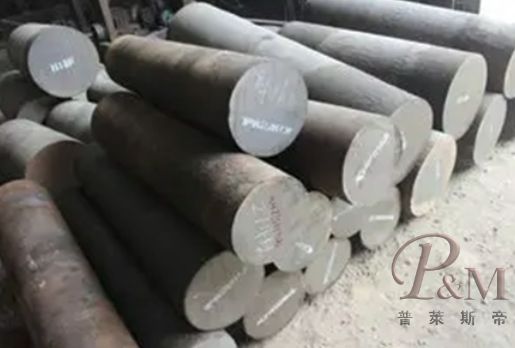
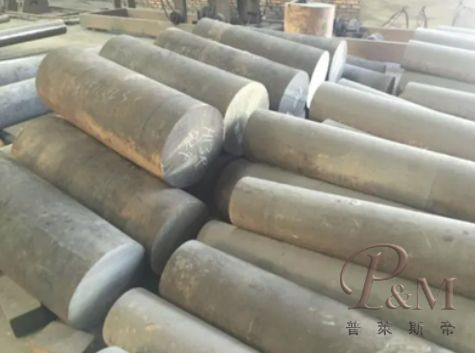
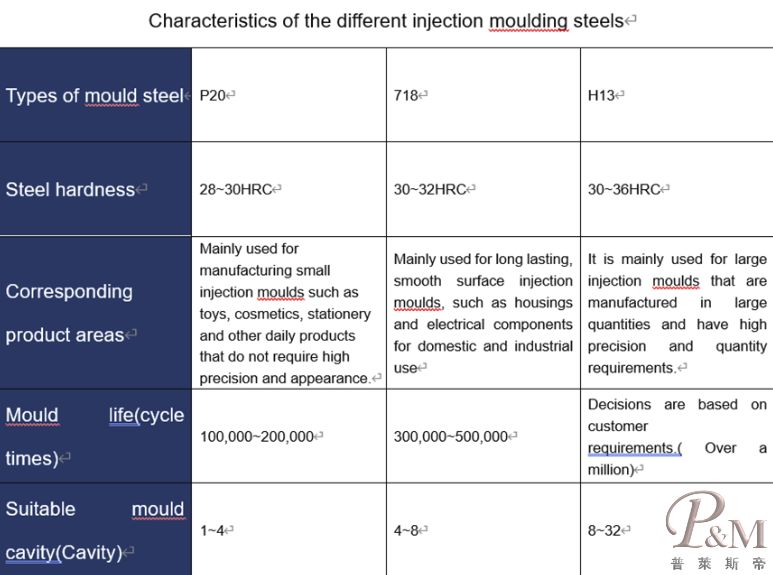
3. Cavity confirmation.
The parts that make up the product space are called molded parts (i.e., the mold as a whole) and the parts (of the mold) that form the outer surface of the product are called cavities (Cavity).
In general, a larger number of cavities in a mold means that it can produce more products in a single injection, i.e., a larger production volume. However, the cost of the mold will also increase, so the number of cavities in the mold must be rationalized according to the amount of production to be achieved.
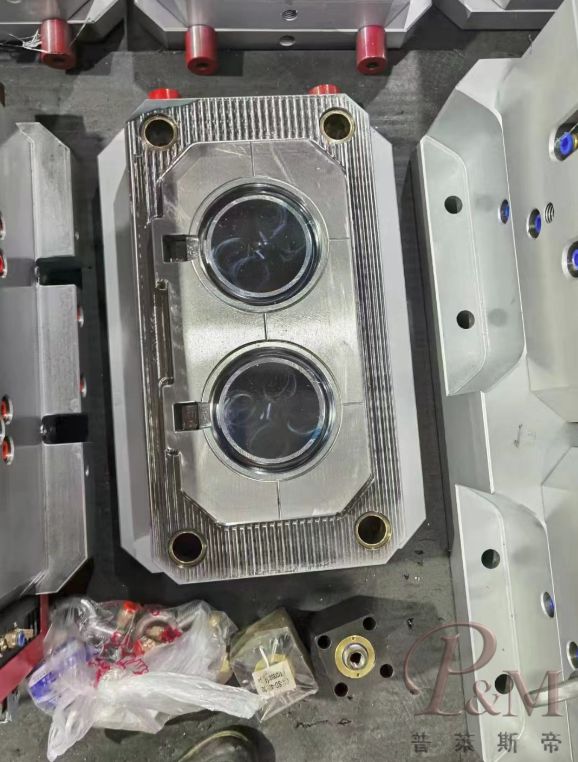
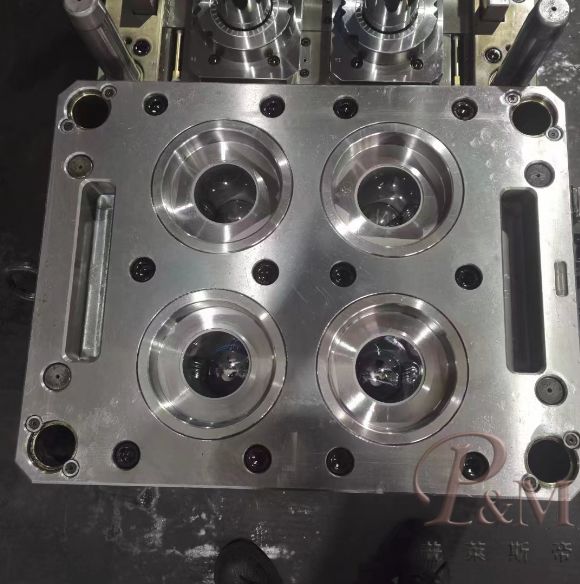
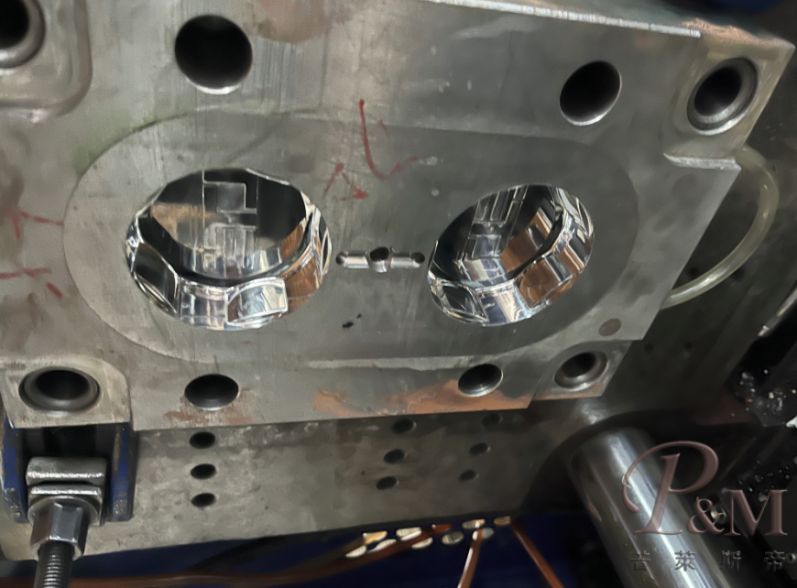
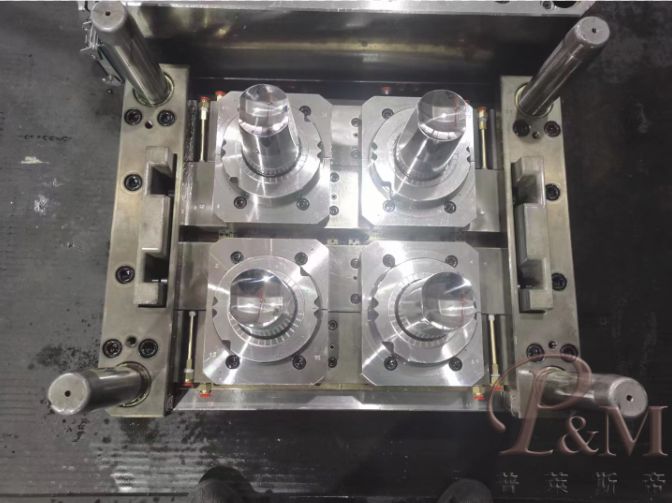
Manufacture of the mold
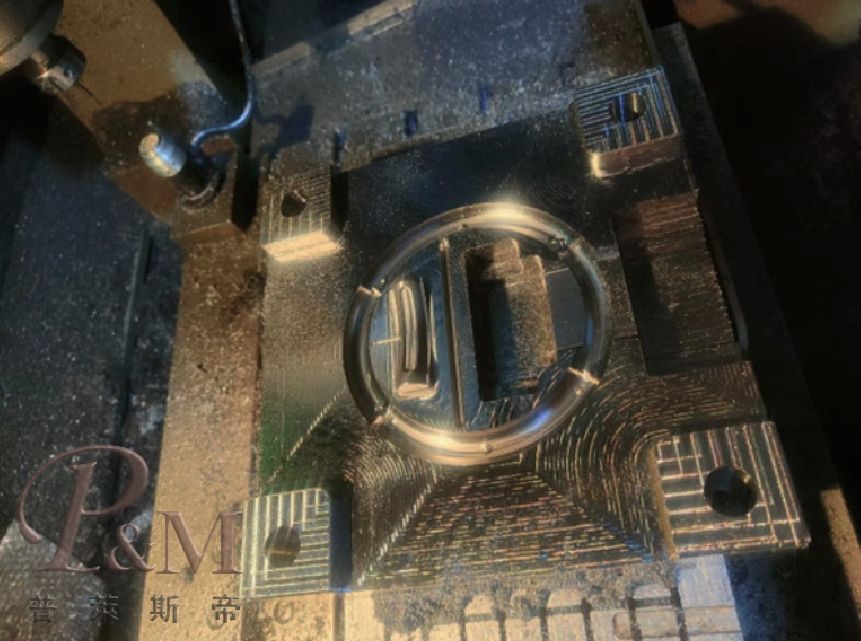
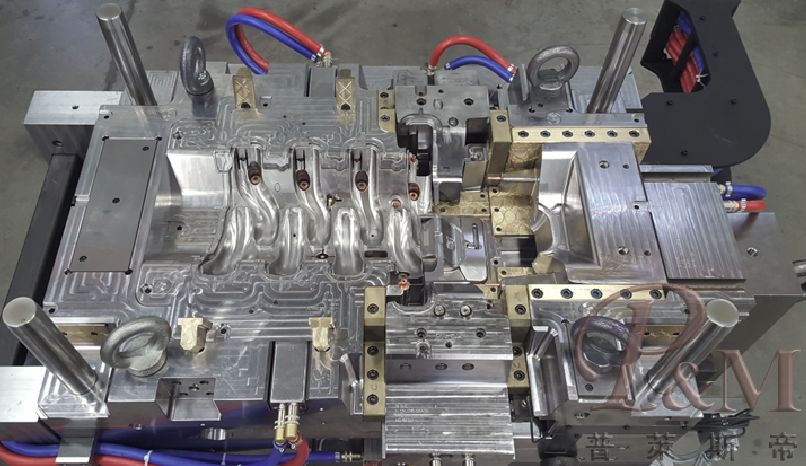
The machining of mold includes CNC machining, EDM machining, wire cutting machining, deep hole drilling machining and so on. After the mold embryo and material are ordered back, it is only rough processing state or just steel material, then a series of mechanical processing must be carried out according to the design intention of the mold to make various parts.
1.CNC machining: its requirements include a variety of processing procedures, tool selection, processing parameters and other requirements, interested in finding relevant information to learn.
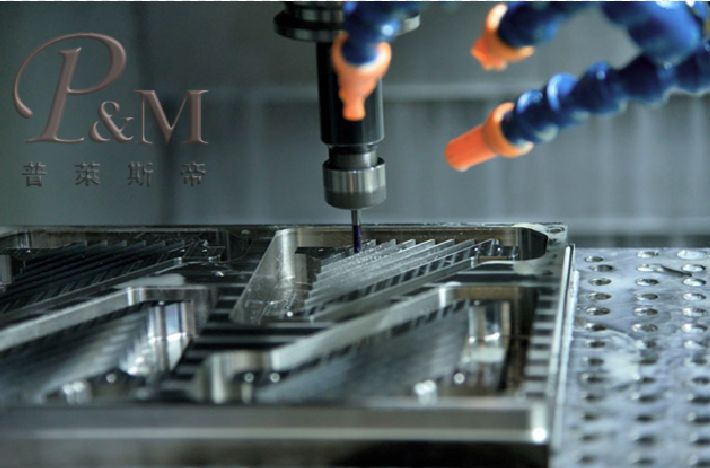
2. EDM machining: EDM is electric discharge machining, which is the process of using electric discharge to corrode the material to achieve the required size, and thus can only process conductive materials. The electric ji used is generally copper and graphite.
Wire cutting is used for machining sharp corners.
Deep hole drilling is generally used in the processing of large mold water transport hole and the processing of the thimble sleeve hole.
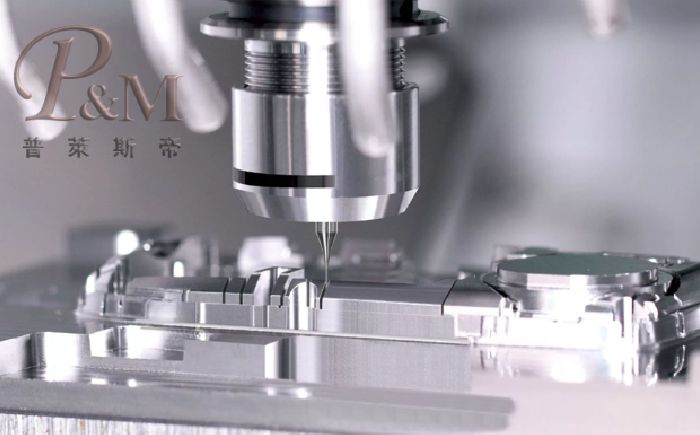
3. Clamp assembly
Clamp in the mold making process plays a very important role, the work needs to run through the entire mold manufacturing process. Clamp work, fit die assembly, turning, milling, grinding and drilling all kinds of proficiency.
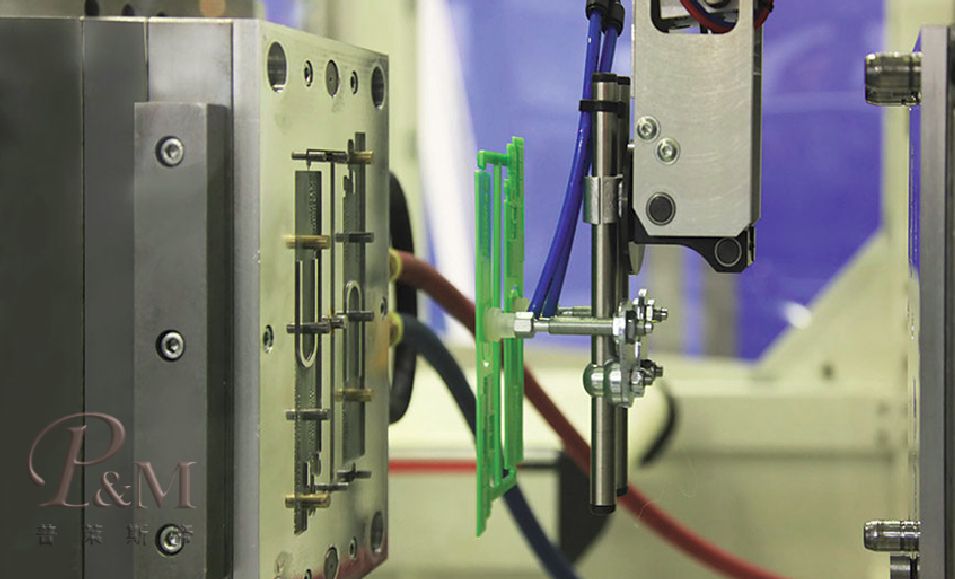
4. mold saving, polishing
Mold saving, polishing is mold in CNC, EDM, clamping processing, mold assembly before the mold using sandpaper, oil stone, drilling plaster and other tools and materials for the processing of mold parts.
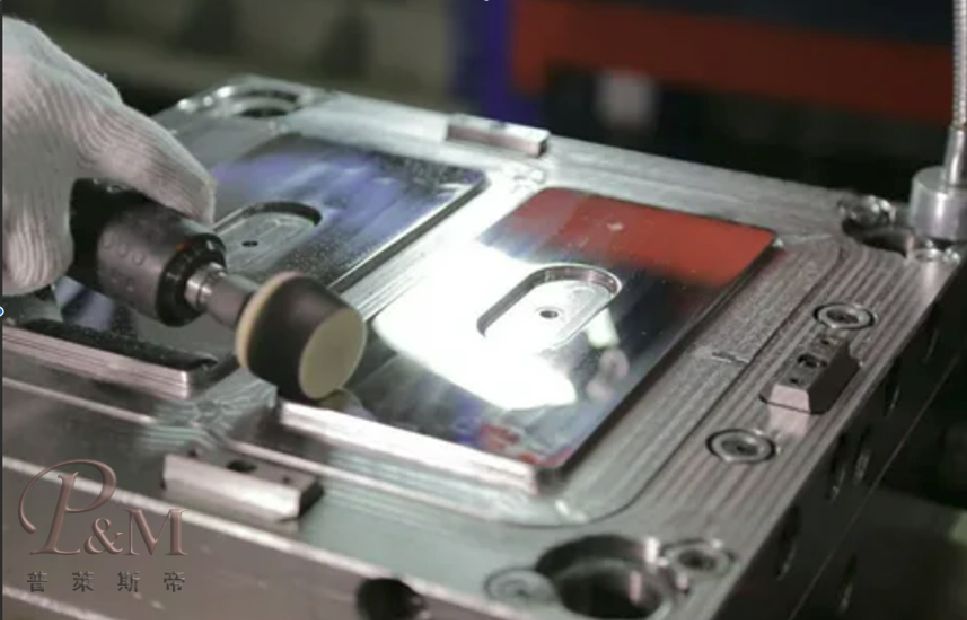
Mold inspection, mold testing, sample to customer
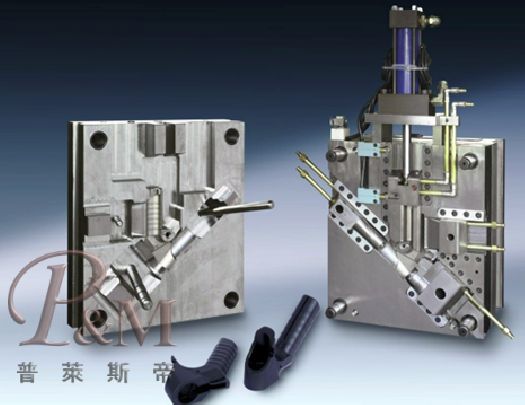
1.Inspection of mold
The process of mold and assembly is actually considered as the inspection process of mold, in the mold assembly, you can check whether the mold frame is in place, whether the thimble sleeve is smooth, whether the mold has done wrong interference, etc.
2.Test mold
After the mold manufacturing is finished, in order to test the mold condition and whether the structure of the rubber parts is good, we need to test the mold on the injection machine. Through the test mold, we can understand the situation of the mold in the process of making beer and whether the structure of the rubber parts is good or not.
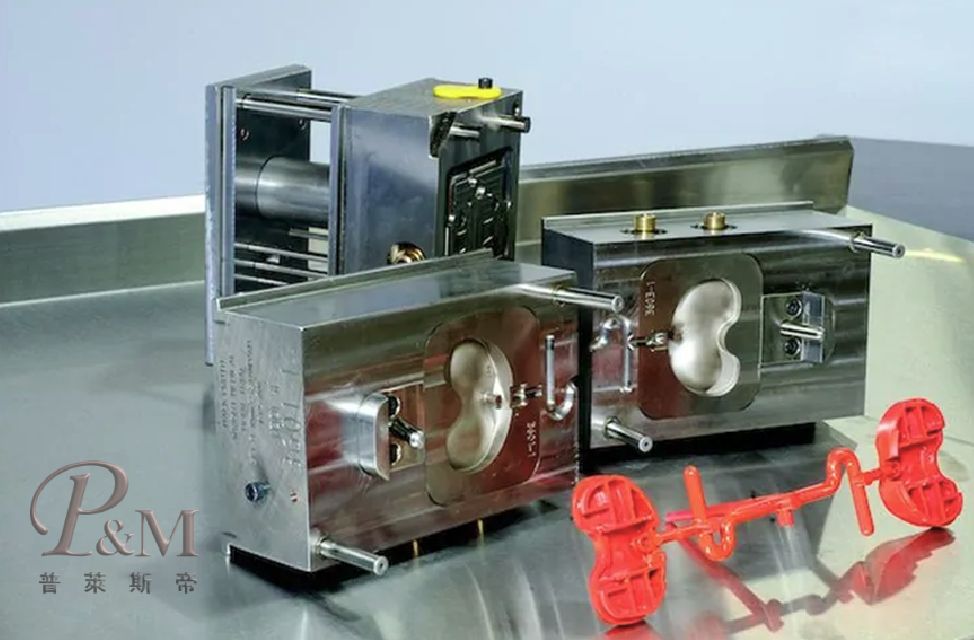
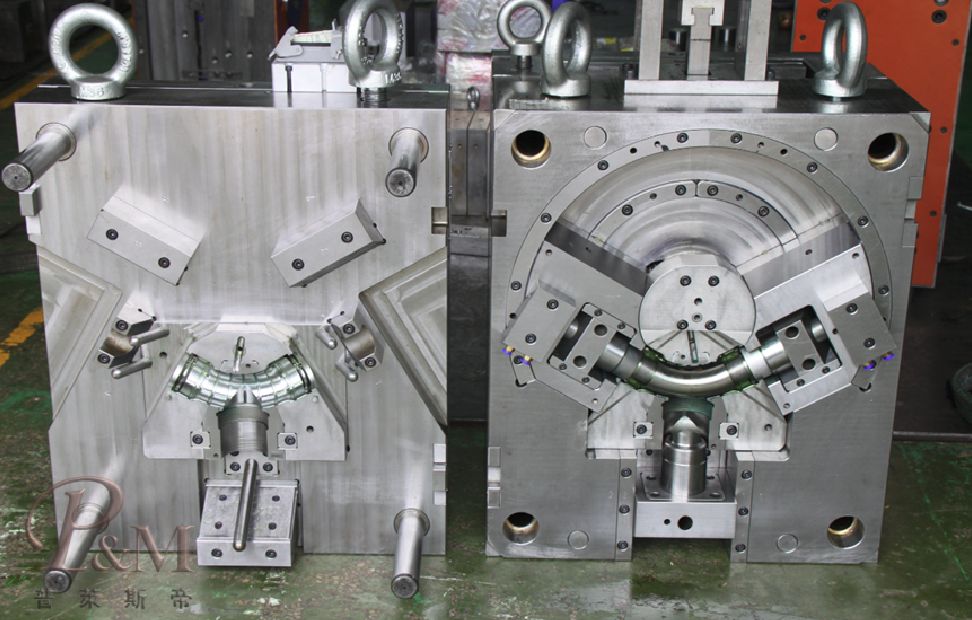
For the requirements of the mold test and the improvement of the defects of the rubber parts, please refer to our tech-worker’s advice.
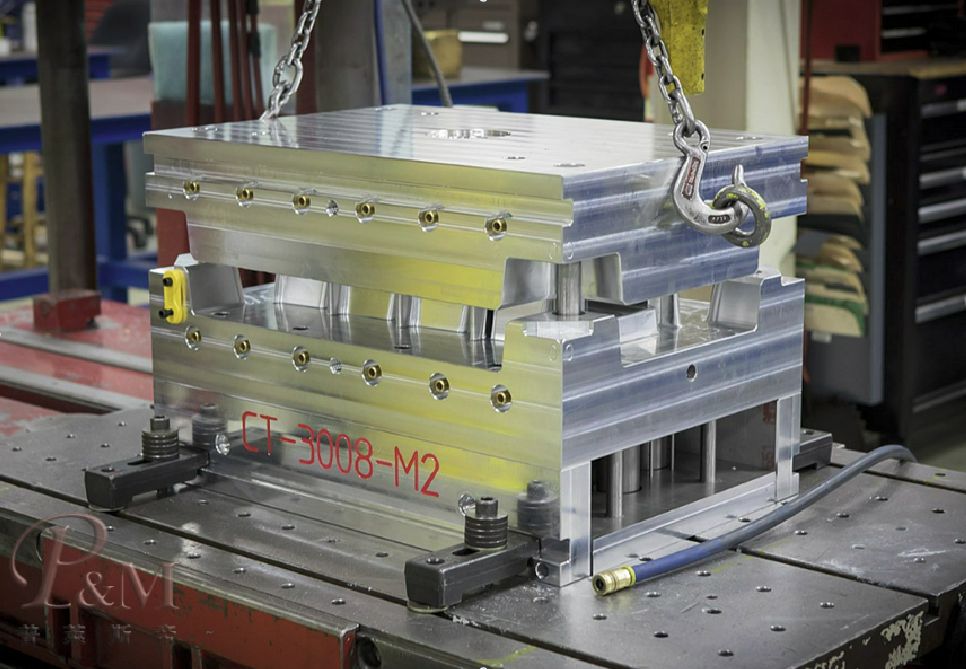
3 Mould modification
After the mold test, according to the mold test situation, we will make corresponding changes to meet the customer's requirements for the mold.
For the structure design, the structure change must try to understand the mold situation, whether to touch the water transportation, ejector pin, how to change easy, etc., can be combined with the relevant information and then make the relevant mold change
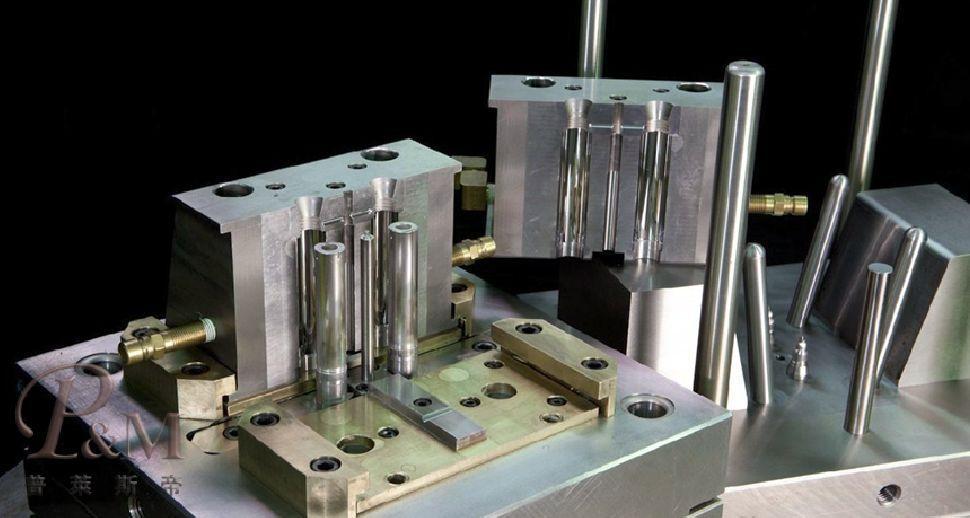
5 Delivery of moulds
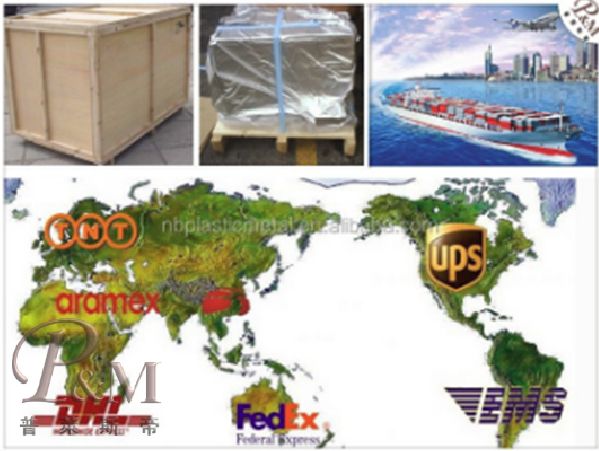
Through cheap and stable transportation channels, we guarantee that the mold will be delivered to the customer's designated location without any damage or delay.
6 After-sales service
Ningbo P&M has a complete sales and after-sales service team.
We offer a one-year mold warranty and complete after-sales service to ensure that our customers can purchase our custom mold service satisfactorily and without worries.
We provide a full range of consulting services prior to purchase so that our customers know what they need.
Our mold design philosophy is based on precision, high speed, durability, stability, energy saving and user-friendly operation, and we are committed to developing many types of precision injection molding machine models. In terms of mold quality control, in order to give users the best experience, we insist on using imported mold components and each assembly step is tested by engineers with precise measuring equipment to ensure that each structure works stably, smoothly and safely. In addition, in order to give you more precise suggestions for your needs, we will analyze your product characteristics, production output and the problems you are currently facing, evaluate all aspects of your situation and give you suitable suggestions. If you want to develop a new product but lack the plans to build a production line, we are also happy to help you by giving you the expertise and technical access to meet your needs.
We have a professional mold commissioning department to test the molds.In addition, we help our customers integrate automation equipment into their molds to ensure that every function runs smoothly, thus ensuring that the mold is delivered to your company ready to start operating immediately.
When you encounter problems during the operation of the mold, our online after-sales team is ready to provide repair services. You can contact us, describe the problem, and our technical specialists will give you a solution as soon as they understand the problem.
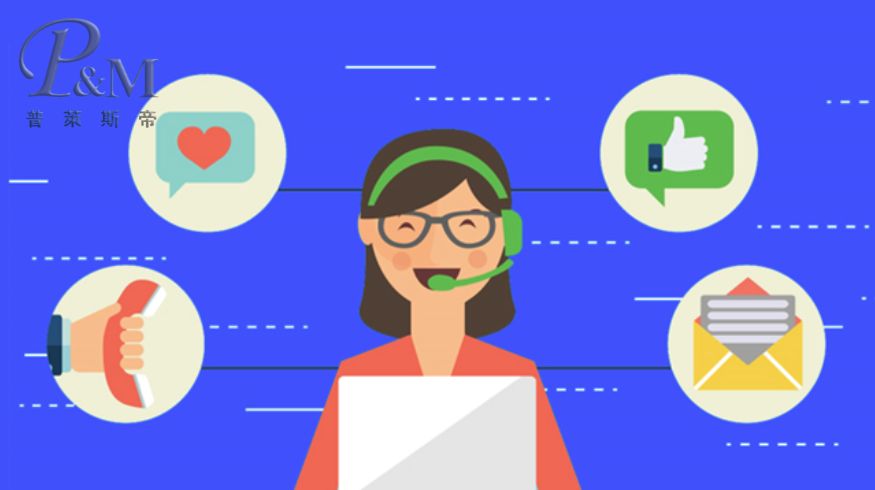
We will bring you the most extreme and perfect service!
At the same time adhering to the concept of long-term cooperation, we are willing to give you the lowest price under the same quality!
Hope to accompany your company to progress and develop together, become your true partner and friend, and achieve a win-win situation! Welcome to inquiry:)